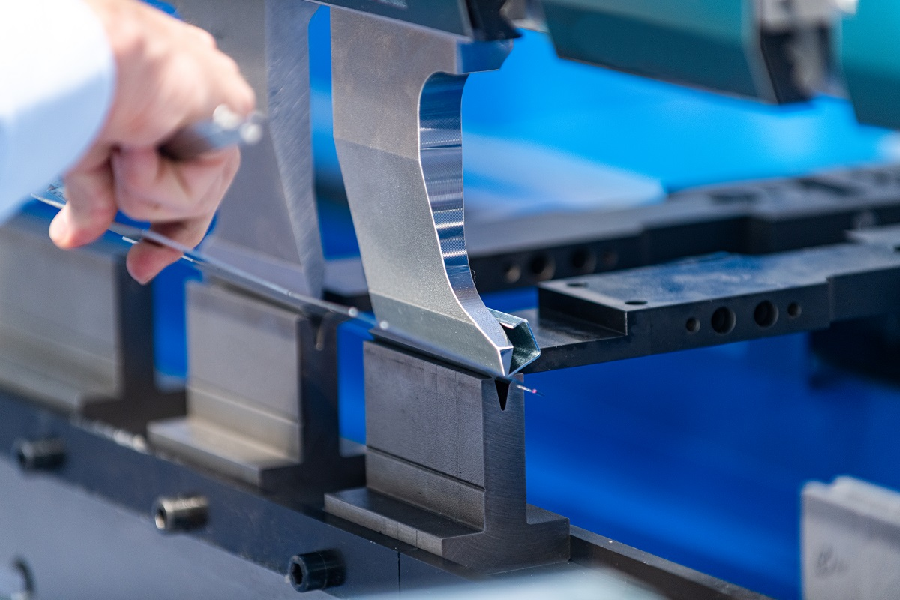
Top Benefits of Press Brake Machinery
Press brakes help fabricators to put together a variety of parts, including brackets, channels, structural forms, enclosures, ductwork, and custom projects. Used in every fabrication service center and workshop, they are an essential tool. press brakes prove particularly helpful for fabricators and operators of manufacturing and industrial plants, as their application spreads across all periods of the production cycle. Let’s start by explaining press brakes.
What are press brakes?
A press brake’s main function is that a durable punch is mounted on a device called a table, and a sheet or plate metal is deposited on it, one press brake operation. By utilizing the die’s force, the material is pressed into the die, causing a flange to be shaped until the desired shape is achieved.
These are the top benefits of press brakes:
In-House Forming Capabilities
If you’re making your manufactured items outside your organization, you have likely encountered press brakes designed to supply maximum precision, which in turn contributes to the production of high-quality items. This affects rejection rates and customer returns.
Reduced material wastage
There are other machines that have to use a lot of material to smoothly curve the items. As brakes absorb less material, they result in a reduction of wasted time.
Punching
If you want to be able to punch a circular series of holes in a part using a press brake, you can effortlessly fit it with a press brake combination or a complete die set that functions with a series of punches. Breaking requires the use of up to 70% of a machine’s strength. They can also be designed to work in parallel with other punches so that the punch stations can be run throughout their whole line previously considered.
Hemming
Manufacturing shops usually need a process of hemming. Hemming is folding a very small portion of the sheet over and then folding it back on itself, thus creating more thickness and strength to the edge while also creating a rounded edge for safety when moving items. Hemming is used to make all kinds of things including covers, containers and panels. Hemming can take place using a specialized hemming hand or a mold on a basic level.
Complex Forming
Press brakes are designed to give you unbridled freedom. Combined with segmented punch and die sets, acute tooling and sophisticated controls, a press brake can make complex angled parts quickly.
Production Bending
Using a CNC control is the best way around a press brake to repeat the actions mechanically many times. When creating a production, if you catch the forming process during the set-up, you can consider a press brake to prevent variable angle and length flanges.
Prototype Forming
Another great benefit of press brakes is that they are uncomplicated to set up and set up, enabling you to quickly make adjustments between various tasks without difficulty. Forming prototypes and skinning applications are also a simple process. An individual working with a press brake can aid paintings to be assembled without expensive or challenging tools or setups.
Conclusion
Press brakes are used for a wide range of applications. They provide outstanding control and accuracy, and they are faster and more productive than other bending processes. When you need fast, high-quality, efficient metal bending, press brakes are the perfect machines to get the job done.